Stability
Slope stability of planar slides and translational slides
|
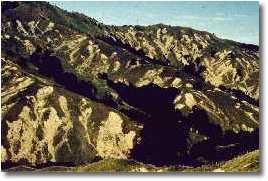
Hillsides
after Cyclone Bola
East Coast, New Zealand.
View large image HERE
|
|
Planar
slides of weak rock which overlies competent or stratified rock
with bedding parallel to the slope can be modelled quite simply.
The normal stress acting on a unit area of the slip surface between
the two rock material is a combination of the normal stress
(sn) and shearing stress (t) (Fig. 3). The magnitudes
of these factors will depend on the thickness (T) of the
slab. For the driving forces to equal the resisting forces, i.e.
safety factor N = 1 (Costa and Baker 1981):

where
tn is the initial shear resistance of the slip surface
and tan F is the characteristic angle of internal friction of the
material. Both these factors would have be estimated or established
using engineering tests.
Figure
3.
If
we consider that there is no initial shear resistance of the slip
surface, tn = 0, then for the slope to remain stable
increasing slope angle, a, must define a relationship of increasing
normal stress, sn, with shearing stress, t, (dashed line,
Fig. 3) which must be less than the failure line, A, which
is equal to the internal angle of friction of the slab material.
Once the slope becomes steeper than the internal angle of friction,
FA, failure will occur for any slab thickness.
If
the slab has a lower angle of internal resistance, but some initial
shear resistance, the failure line, B, will intersect the
shearing stress line at a particular critical normal stress,
sc, (provided that FB < a.).
This critical stress is produced by that precise thickness of slab
material that, if exceeded, will create shearing stress along the
failure surface. To maintain a stable slope in this case requires
that the slab must be thinner than this critical value.
In relatively homogeneous material with no internal bedding of
lineations the failure plane will often assume a circular shape
and will form a slump. Such a failure can be expected when the thickness
of the material likely to fail is greater than the height of the
slope. The failure plane will be some unknown slip surface, usually
curved, along which resisting forces : driving forces is
minimum.
Method of moments
Figure
4.
The
method of moments assumes that failure along the arc will occur
as a lever action about the arc centre (Fig. 4). Hence the
resisting factors are the shear strength, Tc,
of the material times the length of the failure surface, L,
as displaced by radius R from the arc centre. The horizontal
driving forces are displaced by the distance, x, between
the centre of gravity of the soil mass and the centre of a circle
that defines the failure arc.
The
acting moment of the driving forces is a product of the total weight
of the potential slump and x. The safety factor is calculated
as follows:
Failure may not occur on the plane identified in Figure 4 and trial
and error will identify the arc which has the lowest safety factor,
and this arc is the one that should be used in design as it is the
arc along which failure is most likely.
Method of slices
In
the method of slices the slope is divided into vertical slices and
the stability of each slice evaluated (Fig. 4). The safety
factor is calculated as:
Where
S is the normal component of slice weight, T is the tangential
component of slice weight, F is the friction angle for each slice
(determined by laboratory tests and Ts is the
cohesion along the arc (also determined by laboratory tests). As
in the method of moments calculation a number of different calculations
will need to be made to identify the arc surface which is most likely
to fail. These calculations are often made using a computer.
|